Injection moulding is a type of manufacturing technique that involves injecting molten plastic into a mould. This process is used to produce parts with a high degree of accuracy. The plastic car battery case mold is one of the products that can be produced from this process. However, the mould must be designed and manufactured in a way that ensures consistency and efficiency.
When looking for a supplier of car battery case mould, you should consider the company's experience and track record. They should also be able to provide pricing, delivery time, and the type of mould that you need. You may also want to find out about the type of test that the company performs on the mould, especially if the mould is for a high-volume production. If the mould requires a lot of testing, you'll need to make a series of trials to see whether it's suitable for your project.
A car battery case is a part of a car that contains the battery. The case is usually made of polypropylene resin. While this material is recycled at a fairly high rate, it's not as common for it to be recycled as HDPE. Instead, it's often discarded.
As with any injection mould, the design of the car battery case mould is key. The design should include cooling channels, which allow the melted plastic to solidify in the desired shape. Also, the mould should be clean and free of debris. It should also have lubricated moving parts. These parts should be degreased and cleaned regularly.
The size of the mould is also important. The size of the mould determines the number of parts it can produce. More complex moulds will also have more cooling channels. Additionally, a more advanced system will be capable of ejecting parts from the mould. For this, hydraulic devices may be used.
A hot runner system is another option. Hot runner systems are typically more efficient and cheaper. They remove the need for a separate runner, but you may have to do more maintenance on the mould. On the other hand, a cold runner system relies on a separate channel for the plastic to flow through.
The runner of a car battery case mould is designed to ensure that the melted plastic is pushed from the injection moulding machine to the cavities in the mould. The runner can be a hot runner or a cold runner. Cold runner systems are not as efficient as hot runner systems, but they can be more cost-effective.
The mold must also be able to maintain its quality and function over a period of time. For this reason, the mould must have lubricated moving parts and a coolant system. Molding the mould can take weeks or months. Depending on the complexity of the mould, it can take up to tens of thousands of dollars.
A plastic car battery case mould needs to be manufactured with high-quality materials and advanced techniques. It should also be able to withstand high temperatures and pressures. Furthermore, it should be easy to maintain.
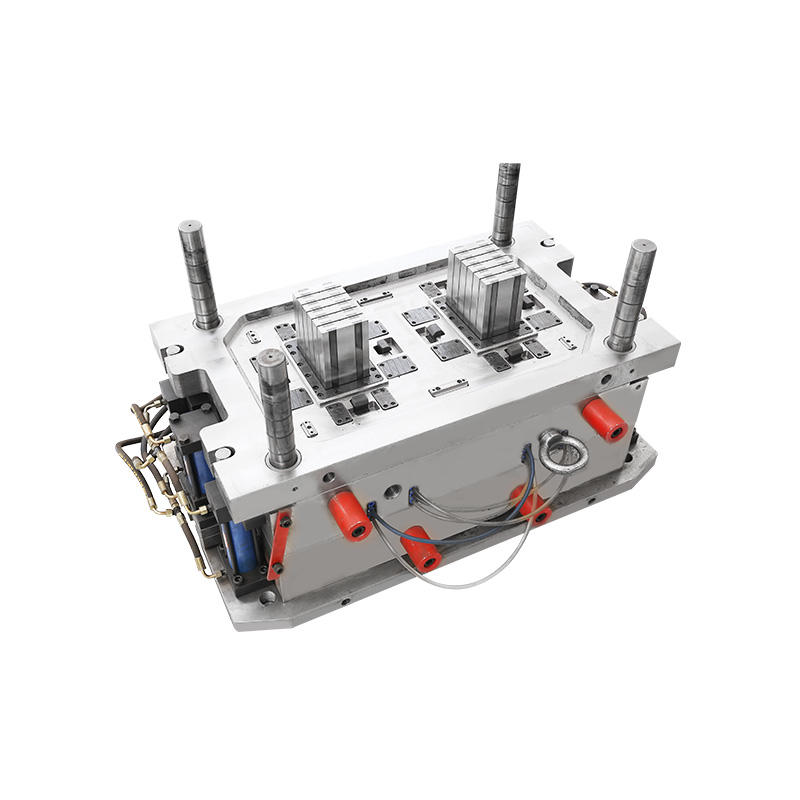
55Ah 66Ah Communication Battery container mould
Car Battery Housing Plastic Injection Mold
● Car Battery Housing Plastic Injection Mold Cavity:
2 Cavities for Battery Container.
● Car Battery Housing products material:
PP, ABS, FR-ABS which is insulated and able to bear high voltage testing
● Car Battery Housing Plastic Injection Mold Main Material:
1.2738 HRC30˚±2˚.
● Car Battery Housing Plastic Injection Mold Ejection System:
Ejector Pin.
● Car Battery Housing Plastic Injection Mold Cycle Time:
60 ~ 70 Seconds.
● Car Battery Housing Plastic Injection Mold Features:
High Polish.
● Car Battery Housing Plastic Injection Mold Running:
1 year Guarantee; Shots guarantee from 300 thousand to 500 thousand under the normal operation and period maintenance.
● Car Battery Housing Plastic Injection Mold Delivery Time:
45 ~ 60 working days to T1 sample delivery.