In the automotive industry, the car battery shell mould stands as a crucial component in the production of vehicle batteries. This precision-engineered mold plays a pivotal role in shaping the outer casing of automotive batteries, ensuring durability, reliability, and optimal performance. In this article, we explore the significance of the car battery shell mould, its advanced features, and the indispensable role it plays in delivering automotive power with precision and efficiency.
Shaping the Backbone of Automotive Power
The car battery shell mould is responsible for molding the outer casing of vehicle batteries, providing the structural foundation for automotive power storage. It plays a critical role in ensuring the safety, stability, and integrity of the battery's architecture.
Precision Engineering for Consistency
Manufactured with precision engineering, the car battery shell mould ensures consistent and accurate shaping of battery casings. Its sophisticated design guarantees uniformity in each mold, resulting in standardized battery shells for reliable production.
Optimal Material Distribution
The design of the car battery shell mould allows for precise material distribution during the molding process. This ensures that the battery casing has the required thickness in critical areas, enhancing the structural integrity and performance of the battery.
High-Temperature Durability
Automotive battery production involves high-temperature molding processes, requiring molds with exceptional heat resistance. The car battery shell mould is engineered with specialized materials to withstand elevated temperatures, guaranteeing repeated use in demanding manufacturing conditions.
Advanced Cooling Systems
To ensure efficient production cycles, the car battery shell mould incorporates advanced cooling systems. These systems maintain the mold's temperature during production, minimizing cooling times and maximizing production throughput.
Seamless Ejection Mechanism
The ejection mechanism of the car battery shell mould facilitates the smooth release of molded battery casings. This seamless process reduces the risk of defects and ensures consistent, high-quality output during mass production.
Adaptability for Diverse Battery Designs
As the automotive industry embraces advancements in battery technology, the car battery shell mould exhibits adaptability for diverse battery designs. It can be tailored to accommodate varying sizes and configurations, supporting the production of batteries for hybrid, electric, and emerging automotive applications.
Quality Assurance for Battery Safety
The car battery shell mould plays a crucial role in ensuring the safety of automotive batteries. Its precision molding and uniformity result in battery casings that are free from imperfections, reducing the risk of leaks or structural failures.
Industry Compliance and Certifications
In an industry that demands stringent quality standards, the car battery shell mould meets regulatory compliance and often holds certifications to assure manufacturers of its high-performance capabilities and adherence to industry requirements.
Driving Sustainable Practices
With the automotive industry's increasing focus on sustainability, the car battery shell mould aligns with eco-conscious initiatives. It minimizes material waste, reduces energy consumption during production, and contributes to the overall efficiency of automotive battery manufacturing.
The car battery shell mould is an exemplar of precision engineering, driving the production of automotive batteries with reliability and efficiency. As the automotive industry continues to embrace advancements in electric and hybrid technologies, this crucial mold plays an indispensable role in shaping the backbone of automotive power. Its ability to produce consistent, high-quality battery casings ensures the safety, reliability, and performance of automotive batteries, contributing to the future of sustainable and efficient transportation. Embrace the precision engineering of the car battery shell mould and witness how it empowers the automotive industry to meet the demands of the electrified future with confidence and precision. As automotive technology evolves, this critical mold remains at the forefront, shaping the future of automotive power with durability, reliability, and optimal performance.
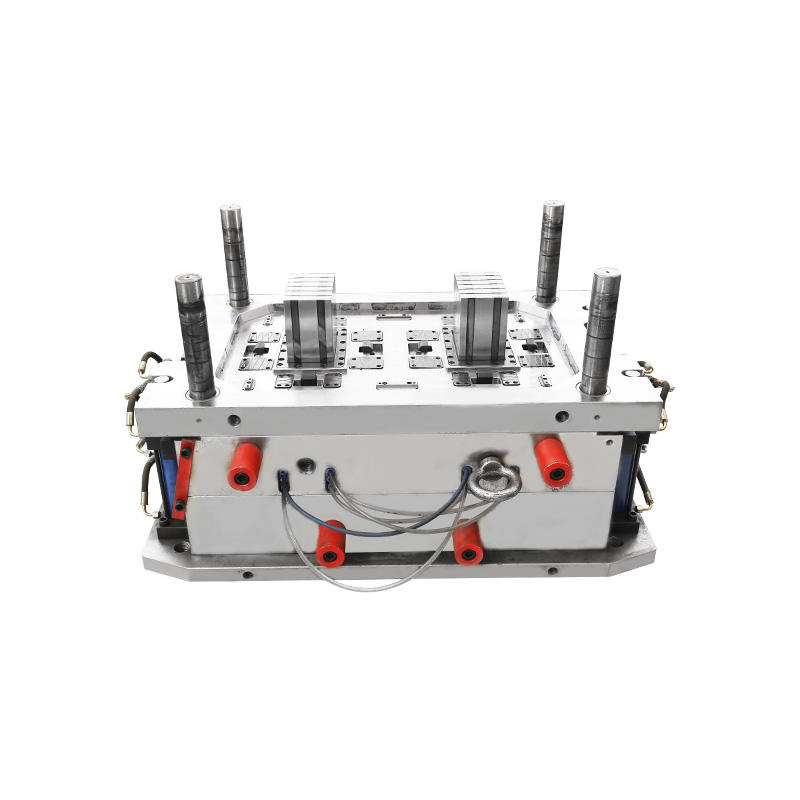
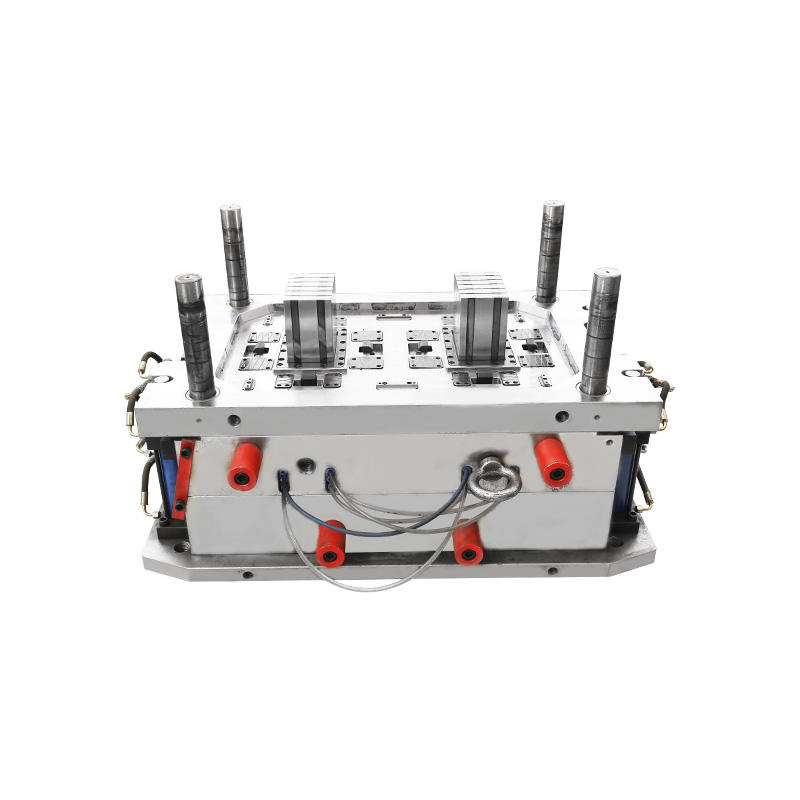