The car battery lid cover plasticmould is a precision tool designed to create high-quality plastic components for car battery enclosures. With its various strengths and features, this mold ensures efficient and reliable manufacturing processes while maintaining strict quality standards.
One of the key strengths of the car battery lid cover plasticmould lies in its selection of mold materials. The mold can be crafted from a range of high-quality materials such as P20H, 718H, 2738H, NAK80, 2316, H13, S136, and 2344. These materials offer excellent hardness levels, typically ranging from 32 to 55 HRC (Rockwell hardness scale). The use of such materials ensures durability, longevity, and resistance to wear and tear, even in demanding production environments.
The mold is designed with flexibility in mind, offering compatibility with various die frame standards. Whether it's the standard die frame, DME, LKM, HASCO, or other specific requirements, the mold can be customized accordingly. This adaptability allows for easy integration into different manufacturing setups and ensures seamless compatibility with existing tooling and equipment.
The car battery lid cover plasticmould offers versatility in terms of cavity configuration. It can be designed for single or multiple cavities, depending on production requirements and volume. Single-cavity molds are suitable for low to medium production volumes, while multiple-cavity molds increase productivity and efficiency, allowing for higher output rates in a single molding cycle.
The ejector system of the mold plays a critical role in the efficient removal of the molded part from the mold cavity. The car battery lid cover plasticmould offers various ejector system options, including motor-driven, hydraulic cylinder, pushing plate, and thimble systems. These systems ensure smooth and reliable ejection of the molded components, minimizing the risk of damage or distortion.
Efficient cooling is vital for maintaining optimal cycle times and ensuring consistent part quality. The mold is equipped with a cooling system that includes core baffle and cavity plate chain-type drilling cooling. This cooling arrangement ensures effective heat dissipation, promoting faster cooling of the molten plastic and reducing cycle times. By maintaining proper temperature control, the mold enables efficient production and helps prevent defects such as warping or sink marks on the final components.
The car battery lid cover plasticmould excels in its precision and attention to detail. The mold is meticulously crafted with high accuracy to achieve the desired specifications and dimensions of the final product. This precision ensures that the molded components meet the required tolerances, resulting in consistent and precise car battery lid cover parts that fit seamlessly into the overall battery enclosure assembly.
Another strength of the mold lies in its ability to accommodate various surface finishes and textures. The car battery lid cover plasticmould can be customized to produce components with different surface finishes, such as smooth, matte, or textured surfaces. This versatility allows manufacturers to meet specific design requirements, ensuring that the battery lid covers have the desired appearance and functionality.
Furthermore, the mold is designed for ease of use and maintenance. It incorporates user-friendly features that simplify mold assembly, disassembly, and maintenance operations. This design consideration reduces downtime during mold changeovers or maintenance tasks, optimizing production efficiency and minimizing production interruptions.
The car battery lid cover plasticmould offers several strengths that contribute to efficient and reliable manufacturing processes. Its selection of high-quality mold materials, compatibility with various die frame standards, flexibility in cavity configuration, options for the ejector system, efficient cooling system, precision and attention to detail, accommodation of different surface finishes, and user-friendly design all ensure the production of high-quality car battery lid cover components. By utilizing this mold, manufacturers can achieve efficient production, consistent part quality, and optimal performance in the production of car battery enclosures.
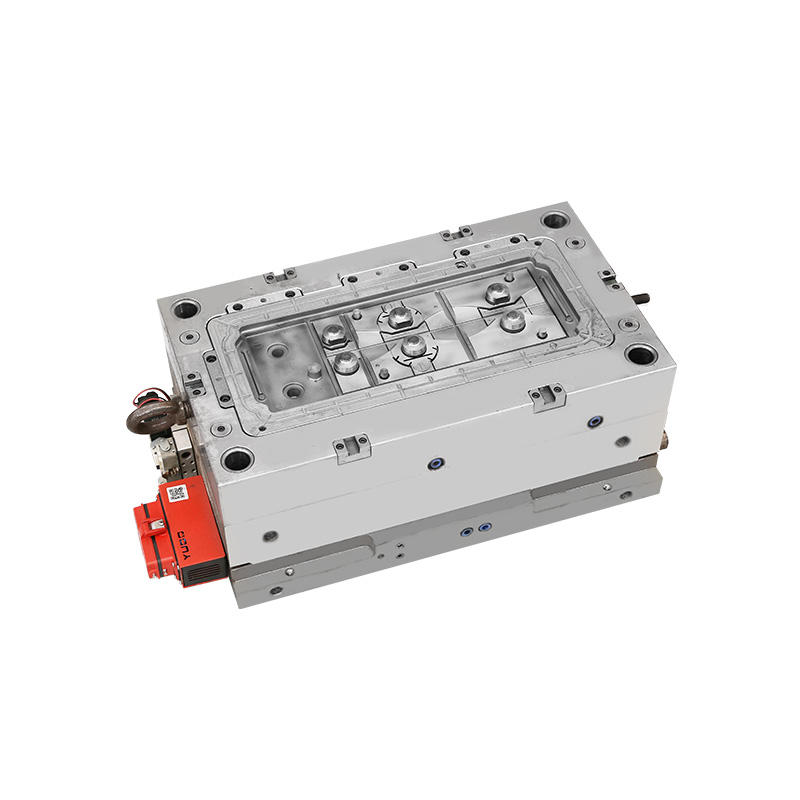